
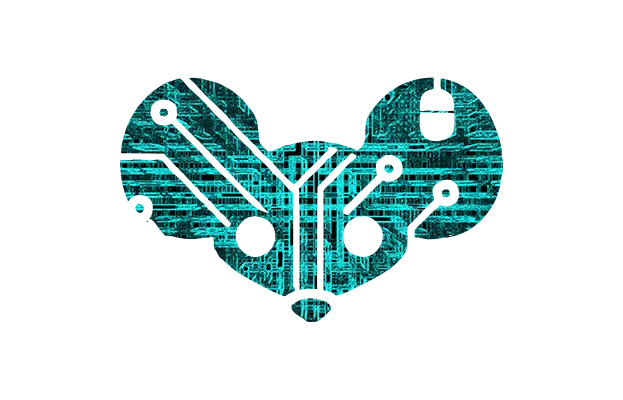
If this passes for the military, then that will mandate the creation of a parts supply chain, as well as documentation and manuals for maintenance and repair, for whatever the military buys. Once that stuff is created, it’ll be a lot easier to mandate that the existing stuff be made available to the public, too.
That might not make much of a difference for a guided bomb, but it’ll make a huge difference for the huge amount of commercial off the shelf stuff that the military buys: laptops, routers, tablets, phones, civilian vehicles, tools, other basic equipment.
As I understand it, MacOS’s desktop relies on GPU instructions that haven’t been implemented in any non-MacOS hosted virtualization environment. So you can have a MacOS VM running on a MacOS host just fine, but you can’t run a MacOS VM in a Linux host, even on official Mac hardware, at least if you want the actual desktop environment. The Asahi Linux people have mentioned it before.